日记名称:学术学者杂志
文章类型:研究
收到的日期:2018年8月29日
接受日期:2018年9月12日
发布日期:2018年9月20日
引文:Yousufuddin S(2018)具有不同挡板间距布置的壳体和管热交换器的传热增强。SCH J APPL SCI RES。第1卷,ISSU:6(50-56)。
版权:©2018 Yousufuddin S.这是在创意公约归因许可证的条款下分发的开放式文章,其允许在任何媒体中不受限制地使用,分发和再现,只要原始作者和来源都被记入。
抽象的
出于传热增强的目的,通过考虑挡板间隔和挡板来改善壳管和管热交换器的构造。本文的调查是通过手动计算进行的,并且对于单个壳体和两个管进行的,通过热交换器,具有可变数量的挡板间距和25%挡板切割。设计的挡板空间是:出于案例A:382毫米,适用于B:427 mm,适用于C:472 mm,以及案例D:517 mm。在我们的论文中,我们使用Kern方法获得了壳侧计算,并在壳侧观察结果,传热系数减少15.3%,压力损失降低49.4%。在本文中也考虑了Tema标准的一般设计考虑因素和设计程序。此外,商业HTRI交换机套件软件还用于设计绘图目的。
关键词
壳牌和管热交换器,优化,设计,挡板。
抽象的
出于传热增强的目的,通过考虑挡板间隔和挡板来改善壳管和管热交换器的构造。本文的调查是通过手动计算进行的,并且对于单个壳体和两个管进行的,通过热交换器,具有可变数量的挡板间距和25%挡板切割。设计的挡板空间是:出于案例A:382毫米,适用于B:427 mm,适用于C:472 mm,以及案例D:517 mm。在我们的论文中,我们使用Kern方法获得了壳侧计算,并在壳侧观察结果,传热系数减少15.3%,压力损失降低49.4%。在本文中也考虑了Tema标准的一般设计考虑因素和设计程序。此外,商业HTRI交换机套件软件还用于设计绘图目的。
关键词
壳牌和管热交换器,优化,设计,挡板。
关键词
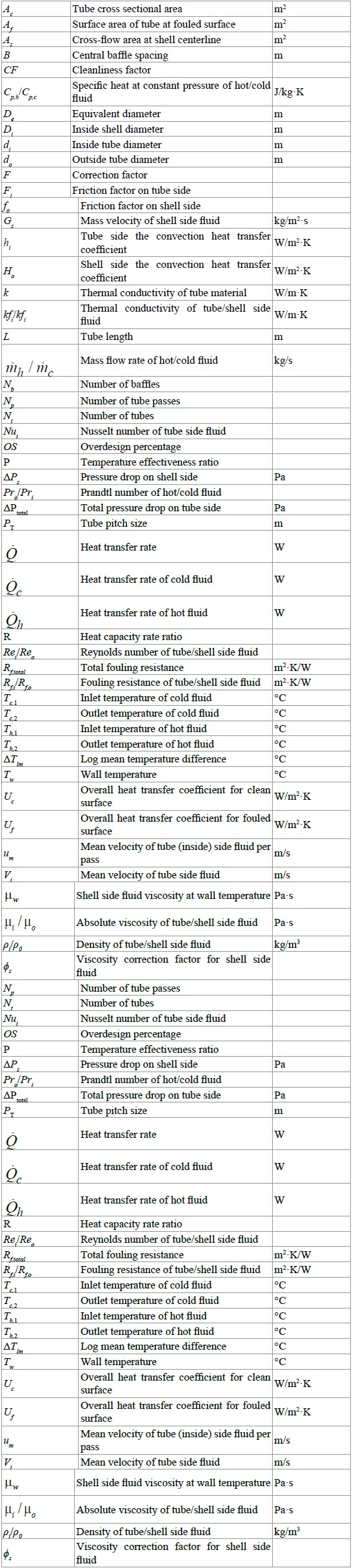
介绍
在大多数工业领域,需要冷却和加热液。用来实现流体之间传热的装置称为热交换器。在大多数热交换器中,流体被传热表面隔开,理想情况下它们不会混合。它被用于许多应用,如空间加热和空调,发电,余热回收,和化学处理[1-2]。通常,它们根据传递过程、流动安排、传热机制、结构、表面密实度、通道安排和工艺流体[3]的相进行分类。
由于管壳式换热器成本低、结构简单、设计灵活,因此在工业领域中最常用的换热器类型是管壳式换热器。管壳式换热器按结构[3]进行分类。这种类型的热交换器是良好的机械布局,有利于加压操作。它由不同类型的材料组成,其中选定的材料用于操作压力和温度[4]。它在发电、炼油、化工和加工工业中有许多应用。用于油冷却器、冷凝器、给水加热器等。管壳式换热器自设计和制造以来,一直存在着影响换热器性能的问题。主要的常见问题是污垢。工程师们高度重视这个问题。污垢是不良物质在换热器表面的聚集,降低传热速率,增加流体流动阻力,导致高压降[3](图1)。
图1:壳牌和管热交换器基本组件。
壳和管热交换器的主要成分是壳,壳盖,管,通道,通道盖,管板,喷嘴和挡板,如图2所示[3]。本文重点关注的主要组成部分是挡板。挡板是安装在用于支撑管的壳侧的板,维持管之间的空间,并以指定的方式将壳侧流体流过或沿管束沿[3]。节段挡板是最常用的。它们通过增强壳侧的液体湍流或局部混合来改善传热通过使壳侧流体以锯齿状方式流过管束。它还增加了压力下降。结果,它需要高泵浦功率,因此它增加了电力消耗[5]。我们已经研究过,测试了挡板之间的中心距离为四种不同的设计。我们已经看到,不同的挡板间距增强了传热速率,被认为是该装置中最常见的问题之一。我们的研究具有生产二乙醇胺和三乙醇胺。 In the production process as shown in Figure 1, after each distillation tower there is a shell and tube heat exchanger.
图2:乙醇胺的流量表生产。
设计方法
管壳式换热器的传热方式通常包括每一种流体之间的对流和通过分隔两种流体的壁进行传导。在对管壳式换热器的分析中,可以方便地用一个整体传热系数U来表示所有这些传热模式的贡献。换热器中某一位置上两种流体之间的换热速率取决于该位置上的温差大小,而温差在管壳式换热器上是不同的[6,7]。
因此,在热交换器的传热分析中,方便建立热和冷流体之间的温差平均值,使得总传热速率在流体之间,并且可以从[8]中确定。
地点:
A是总热侧或冷侧传热区域。
u是基于该区域的平均整体传热系数。
LMTD(对数温差)方法非常适合于确定热交换器的尺寸,以实现热和冷流体的质量流量,入口和出口温度[8]。
地点:
ΔT.1= T.H,1-T.C,2
ΔT.2= T.H,2-T.C,1
对于多通道和交叉流热交换器,对数平均温度差应使用修正因子(F)进行修正。F是无量程的,它取决于温度有效性P,热容率比R和流动安排。
地点:
图3为一壳二管道次的管壳式换热器的修正系数。
图3:具有一个壳管通道和两个或多个双管通道的管壳式换热器的LMTD修正因子F。
对流换热系数h取决于流体的物理性质和物理情况。管侧对流换热系数hi可由(5)计算,壳侧对流换热系数hₒ可由Kern法(6)确定。
总换热系数表示一种流体向另一种流体传热的总阻力,它受传热介质的厚度和导热系数的影响。系数越大,热量就越容易从热源转移到被加热的产物上。它分为[8]两部分。
•洁净表面的整体传热系数
•污垢表面的整体传热系数
在RF,总计总污垢阻力为
设计师简单地增加了一定百分比的清洁表面区域,以考虑污垢。根据清洁表面总传热系数,添加的表面隐含地固定了总污垢阻力。过度指定百分比不应超过约30%(10)。此外,清洁度因子是一个重要的术语清洁度因子是术语,当热交换器污染时,术语涉及整体传热系数。这种方法提供了一种与清洁表面总传热系数(11)直接变化的污垢津贴[9]。
因此,可以从(12)获得计数器流量的传热速率。
当流体流过热交换器时,通常会在流动方向上(在流体速度降低的一些特殊情况下,压力可能增加)。在流动通道,喷嘴,歧管和热交换器的集管中发生压力下降,并且必须评估这些压降中的每一个,除非经验表明可能忽略一个或多个[10]。
管侧压降可由(13)计算。
通过方向的变化引入了额外的压降ΔPR.,可以通过(14)得到。
因此管侧总压降为:
壳侧压降取决于流体通过管束的管数,在挡板之间以及每个交叉的长度[8]。
确定挡板间距和挡板切割
挡板间距是相邻挡板之间的中心线到中心线距离,并被识别为影响壳体侧面设计上的压降和传热特性的最重要的几何参数。它影响壳侧流体的速度,从而影响传热,较小的挡板间隔,较小的流量面积和流体速度越高。流体速度的这种增量表示摩擦压降和传热系数的增加。虽然,减少挡板间距增加传热系数,但由TEMA标准设置的较低限制,壳体直径为55,从未小于2(51mm)。如果挡板间距较高,则传热系数降低。此外,较高的挡板间距导致纵向流量,其比交叉流量和大型无支撑管跨度较低,这将使热交换器由于流动引起的振动而容易发生管道故障。最大挡板间距也由Tema标准通过机械考虑来指定。这是因为除了提高传热系数之外,挡板的目的也是支撑管。
热交换器设计者必须选择挡板间隔,以执行传热系数的最大可能值,而不超过壳侧流体的允许压降。挡板切割表示为壳体内径的百分比,在15%和45%之间变化。最常见的挡板切割约为25%。由于偏离理想情况,非常小而非常大的挡板削减是对传热的不利。对于低挡板切割,壳侧流体湍流高,因此窗口的流体速度高。结果,传热系数增加。然而,对于大的挡板切割,将存在具有低速度的流体的重要区域,因此低传热系数。减少低于20%的挡板,以增加传热系数或增加超过35%以减少压降通常导致设计不佳。为了实现这一目标,设计人员应该改变管束几何形状的方面,而不是将挡板减少到20%以下的挡板或增加超过35%[10]。挡板切割在与不同挡板切口相对应的壳侧流体流中的效果。 Optimum baffle spacing is somewhere between 0.4 and 0.6 of the shell inside diameter and a baffle cut of 25% to 35% is usually recommended.
结果和讨论
表1和2示出了可用的设计数据和管侧和壳侧流体的特性。
表格1:可用的设计数据。
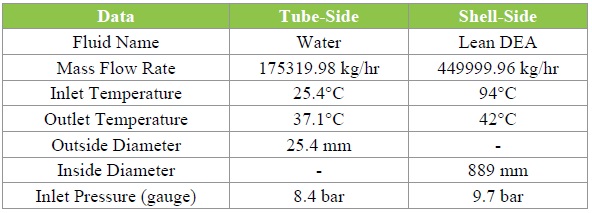
表2:水平温度下水和瘦剂的性质。
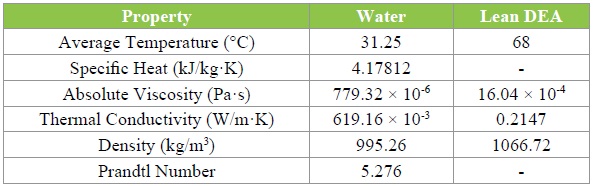
表3描绘了用于管侧的分析计算的恒定值,而表4示出了在本研究工作中考虑的不同设计的不同挡板间距的壳侧计算的简要结果。
表3:管侧的恒定值和两种流体的一些性质。
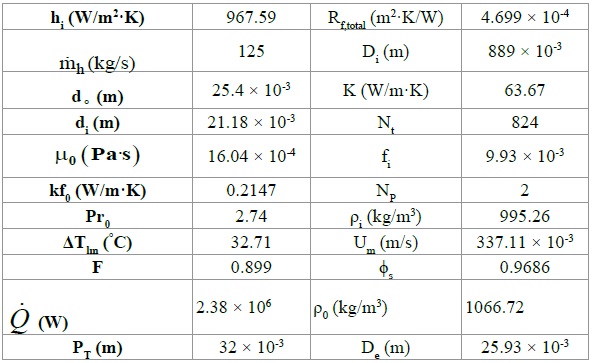
表4:由于不同的挡板间距,不同设计的概述结果。
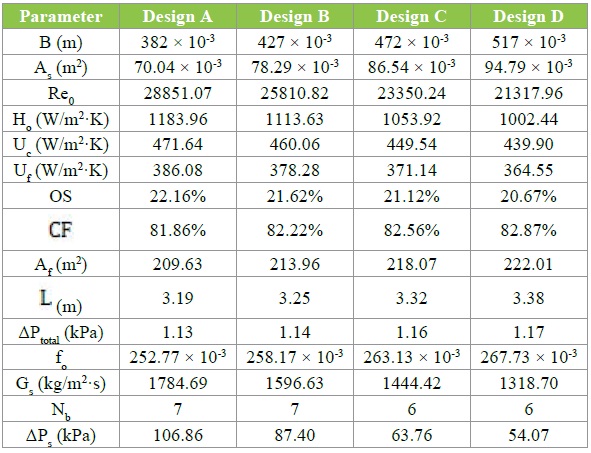
从如表4所示的总结结果,将壳侧传热系数和管侧的总压力与各种挡板间距进行比较,这些挡板间距分别在图4-6中描绘。
图4:壳侧传热系数与挡板间距。
图5:管侧压降VS挡板间距。
图6:壳侧压降与挡板间距。
图4显示了挡板间距对壳侧传热系数的影响,其中壳侧传热系数的最大值和最小值分别为1183.96和1002.44W / m 2·k。很清楚,随着挡板间距的挡板间距,传热系数减小,并且因为增加的中央挡板距离意味着改变流动型。设计A和D之间的雷诺数的百分比减小在湍流区域中26.1%,并且该百分比足以改变流动类型。因此,这导致热传递减少,并且来自流体力学,我们知道高湍流流体导致高热转印。
图5显示了挡板间距对管侧压降的影响,其中管侧压降的最大值和最小值分别为1169.35和1129.05Pa。我们注意到,随着中央挡板距离的增加,压降增加,因为增加挡板间距意味着管长度增加。结果表明,随着管长度的增加,管侧压降增加3.7%。这意味着改变挡板间距不会产生很大的影响管侧压降。
图6为挡板间距对壳侧压降的影响,其中壳侧压降最大值为106.86,最小值为54.07 kPa。从图中可以看出,随着挡板间距的增大,壳体侧压降减小,这是由于壳体流体质量速度引起的。中心挡板间距的增大可使壳体流体质量速度降低26.1%,这一比例足以使壳体侧压降降低50%。
利用HTRI软件进行设计仿真
在这项工作中,我们使用HTRI软件来模拟绘图以获得最佳设计。图7显示了设计侧视图。我们注意到HRTI软件的挡板数量是根据设计D的5,其中根据我们的手动计算的挡板数量为6(表4)。图8示出了所获得的最佳设计D的3-D视图,图9给出了壳和管热交换器的总长度为4495.8毫米(根据TEMA标准)。
图7:管壳式换热器设计侧视图D。
图8:三维壳和管式换热器设计D.
图9:设定壳管热交换器设计D.
结论
在本文中,我们介绍了用于冷却贫乙醇胺的壳体和管式热交换器的细节设计,其被认为是石化植物中的重要液体,特别是用于环境目的。研究了改变交换器对热传递和压降的单一节段挡板间距的影响。因此,我们考虑了四种设计,遵循Tema标准,我们根据传热和压降因子模拟了最佳设计。从结果,我们注意到,在设计A和D之间的传热系数之间的壳体侧减小15.3%,管侧压降增加3.7%,壳体侧的压降降低49.4%。
承认
作者表示他们对朱瓦大学学院的感谢感,KSA的支持延长了开展研究工作的设施。
没有参考